CSIRO and Swinburne level up Australia’s manufacturing sector with Industry 4.0 Testlab
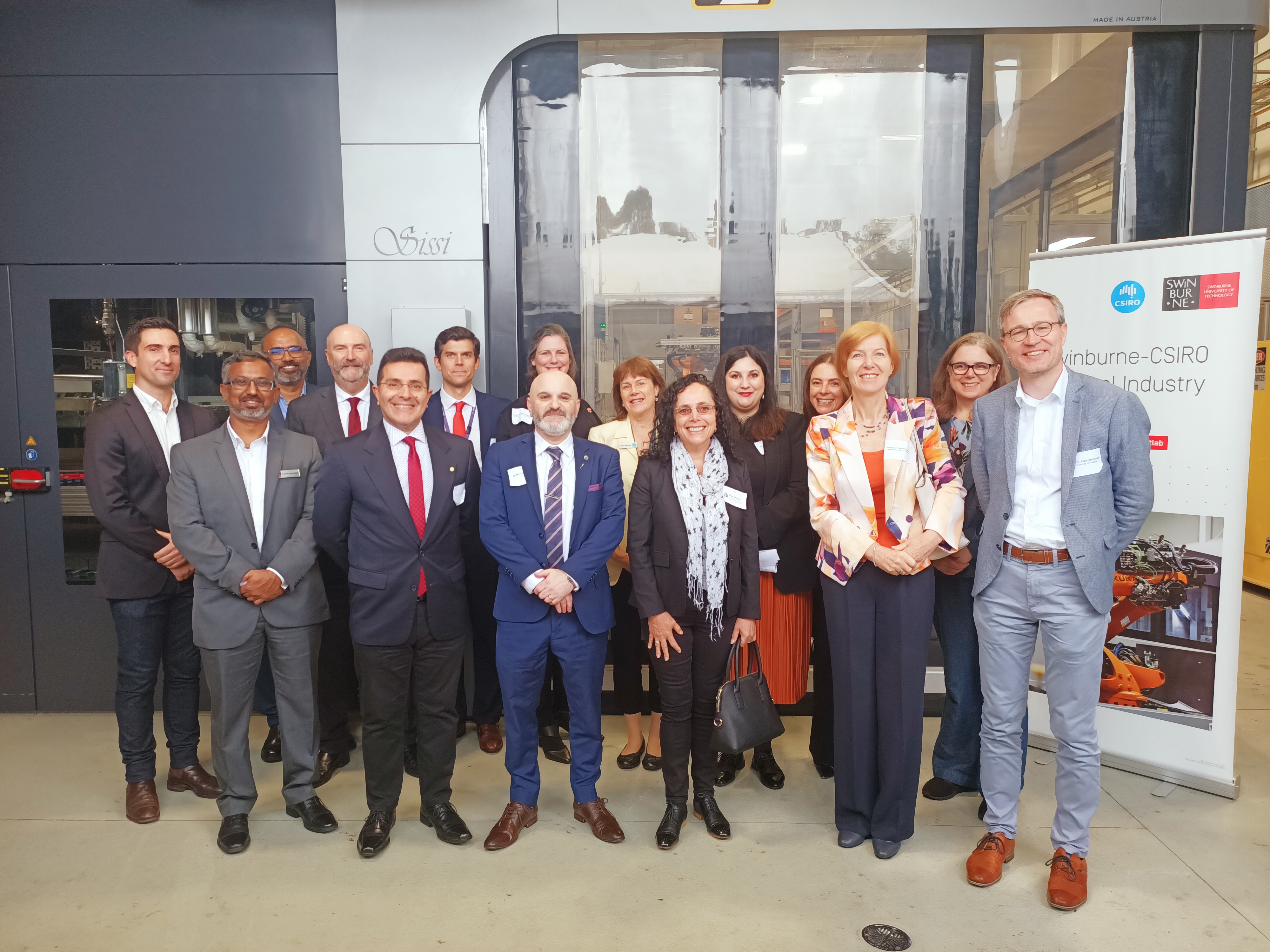
The Testlab has showcased its world-first fully automated industrial-scale production facility using a 3D-printing approach to composite component creation.
In summary
- The future of Australian manufacturing is being built at the Swinburne-CSIRO National Industry 4.0 Testlab
- The Testlab includes a world-first process for the additive manufacturing of carbon fibre composite materials
- Its world-first fully automated industrial-scale production facility uses a 3D-printing approach to composite component creation
The future of Australian manufacturing is being built now at the Swinburne-CSIRO National Industry 4.0 Testlab, including a world-first process for the additive manufacturing of carbon fibre composite materials.
Today, the Testlab showcased its world-first fully automated industrial-scale production facility using a 3D-printing approach to composite component creation.
The showcase was attended by Member for Chisholm Dr Carina Garland MP, one year on from the federal government announcing their Rebuilding Australian manufacturing agenda to revitalise Australia’s industrial capability and manufacturing.
Swinburne Chief Scientist Professor Virginia Kilborn says the university is proud to be one of Australia’s leading partners in the research and development of advanced manufacturing.
“Swinburne continues to deliver ground-breaking digital techniques to push Australia to the forefront of manufacturing carbon fibre composite components. Our tech-led approach promotes widespread adoption of Industry 4.0 standards and digital twins, to help secure Australia’s manufacturing future.”
Based at CSIRO’s Clayton facility, the Swinburne-CSIRO National Industry 4.0 Testlab supports innovative research and development for Swinburne’s Aerostructures Innovation Research (AIR) Hub, Victorian Hydrogen Hub, ARC Research Hub for Future Digital Manufacturing, and collaborations with CSIRO's Data61 arm.
Industry 4.0 Testlab Research Director Professor Boris Eisenbart is thrilled to share the incredible work of Swinburne and CSIRO through the National Industry 4.0 Testlab.
“Testlab is already supporting groundbreaking projects in areas like aerospace, automotive, 3D printing and digital twinning. This is only the start for this world-leading facility, and I am excited for what we can do next to continue to build our partnership with CSIRO and our industry network.”
The Global Innovation Linkages program project is another key initiative of the facility. Developing a highly automated, flexible approach to the manufacturing process, the project integrates world-first 3D fibre printing technology with a unique composite curing process and digitisation technologies. This will achieve a leap forward in increasing the production rates and quality of composite part manufacture, while significantly lowering the cost of production.
CSIRO's Chief Scientist Professor Bronwyn Fox is an integral part of the Swinburne and CSIRO community. Since holding previous positions as Swinburne’s Deputy Vice-Chancellor of Research and Enterprise and Director of Swinburne’s Factory of the Future, she is now also supervising PhD students undertaking projects with the Testlab.
Professor Fox is one of the many world-leading experts who will use this facility for innovative education, research and development outcomes in manufacturing for years to come.
“Australia’s future depends on having a world class advanced manufacturing capability and Testlab has been purpose-built on the cutting edge of what we need to succeed in the era of Industry 4.0," she says.
“It is a facility that gives us the ability to generate, translate and accelerate research, training and technology into opportunities and competitive advantage for Australia."
“Testlab’s real power is collaboration – it brings together the people, the capabilities and the intention to deliver benefits for the nation through generous collaboration between Swinburne, CSIRO and other key players in Australia’s research and innovation system.”
-
Media Enquiries
Related articles
-
- Technology
New research finds Instagram promotes white appearances, cultural appropriation and plastic surgery via filters
New research finds Instagram filters promote white beauty standards, selective cultural appropriation and allow users to ‘try on’ risky surgical procedures.
Thursday 24 July 2025 -
- Technology
- Science
- University
- Engineering
Swinburne to advance battery life and EV cybersecurity with Australian Research Council grants
Swinburne has secured two grants from Australian Research Councils to advance research in energy storage and cybersecurity.
Wednesday 02 July 2025 -
- Technology
- Science
- University
- Sustainability
Swinburne powers breakthroughs in sustainable mining and materials technology
Swinburne innovators have been awarded $4 million in funding from the Australian Government, driving Australia’s future in sustainable innovation through two groundbreaking projects.
Tuesday 15 July 2025 -
- Technology
Microsoft, IBM and Google are racing to develop the first useful quantum computer. Ultracold neutral atoms could be the key.
Swinburne University of Technology has been exploring ultracold neutral atoms for two decades.
Monday 30 June 2025 -
- Technology
Swinburne to harness artificial intelligence to tackle discrimination in sport with adidas Foundation grant
Swinburne is developing an advanced artificial intelligence system to help sporting clubs around Australia tackle discrimination and create more inclusive sporting environments.
Monday 26 May 2025